It is actually difficult to define the quality of hole processingreason
If the hole has strict tolerance or surface finish requirements, secondary processing such as boring or reaming usually completes the hole to the final machining size. In these cases, the main value of a drill bit may be to drill as many holes as possible as quickly, and what users can see is whether the positioning is accurate.
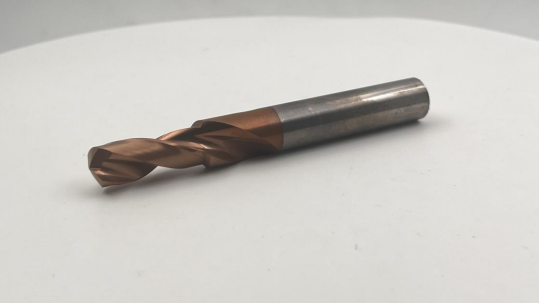
But this is not always the case. In some applications, spending more time and effort may help the drill bit meet quality standards in one operation. Alternatively, it can be determined that the quality of the drilling affects its ability to accept high-quality secondary processing. For example, if drilling at an excessively high speed, heat may cause the material to work hard, which can greatly shorten the lifespan of the tap and even make the material too hard to be tapped.
If a carbide drill bit drills 2 or 200 holes, it may be different; If it is 200 holes, the quality focus may mainly be on the speed (efficiency) of completing the work; If this job only requires 2 holes, spending more time and effort during the drilling process, or using specially designed tools to drill and ream holes in one operation, can produce holes that meet quality specifications without additional processes.
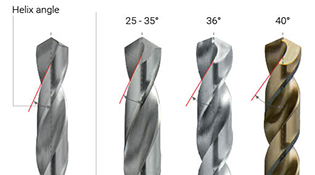
Maybe there are three questions that come to my mind here
1.Whether the tolerance of the hole is met.
2. Whether it meets the requirements for hole processing.
3. Whether the concentricity is good.
Carbide drill bits are actually applied in many fields, but many technologies are also ignored. The design of spiral angles is also very particular, such as low spiral angle or straight groove drill bits, which are very suitable for short chip materials such as cast iron and ductile iron. For example, a spiral angle of 20-30 ° is conducive to universal drilling in various hard materials, as this angle helps to remove chips.
However, aluminum and copper tend to have high helix angles, which provide a predictive effect and aid in chip removal. Choosing drill bits with the correct characteristics for specific materials and applications will extend the tool life and achieve good smoothness.
There are also significant differences in coatings. Usually, for example, some drill bits will use a composite coating that can fully function, including titanium and chromium as well as a titanium silicon layer.
Silicon gives the coating high lubricity, so chips can slip off and avoid the formation of chip buildup. Avoiding chip buildup is the key to maintaining good cutting ability of the tool and avoiding leaving traces on the hole wall.
Some new coatings are combined with higher speeds to remove materials, resulting in pores with good smoothness. These coatings need to be able to withstand the heat generated by high-speed motion.
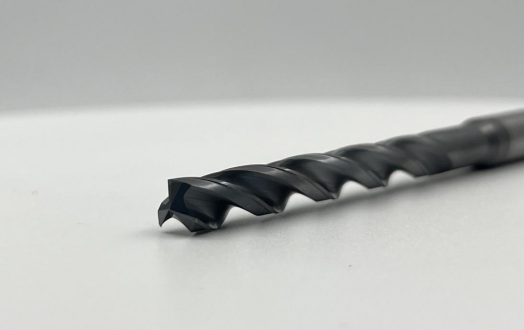
1. Details of controlling the drill bit
The selection of appropriate bars and the quality of holes have already started from the process design. If the runout is too large, it will sacrifice the accuracy, smoothness, and concentricity of the hole. The appropriate core thickness on the drill tip is crucial for maintaining stability when the drill bit is engaged with the processed material, in order to prevent the drill bit from becoming too large and offset, which can cause the hole to become too large or affect its straightness.
When quality requirements include improving tolerance and surface finish, changing from single ligament to double ligament on drill bits can be helpful.
These edges stabilize the drill bit by providing four contact points in the hole and provide a polishing effect to leave a very good finish. The double ligaments can also serve as a guide to keep the drill bit moving forward in a straight line, especially in deep holes. It can prevent the drill bit from getting bigger and shaking, thereby providing a relatively circular hole.
Although a double ligament drill bit produces a good surface in short chip materials, it is recommended to use a single ligament drill bit when the material produces growing chips. For long chip materials such as aluminum or stainless steel, single ligament drills are the preferred choice. Using a double ligament stainless steel drill bit can cause chips to enter the contact point between the drill bit and the material.
Controlling runout is another key aspect of hole quality. Jumping too much can cause the processed aperture to become larger, and as the drill speed increases and rotates, it will cause the drill to drill larger and larger holes.
Long drill bits can lead to poor rigidity and vibration. These vibrations, especially those that are difficult to see with a small drill bit, can cause the drill bit to break and leave a broken blade on the inner hole surface.
2. Control of Cutting fluid
Proper coolant management, including maintaining optimal coolant concentration, filtration, and pressure, is crucial in drilling applications.
An appropriate coolant concentration increases lubricity while taking away the heat from the cutting edge of the drill bit. Filtering can remove metal pollutants and other substances, thereby improving drilling performance and preventing problems such as coolant hole blockage in small diameter drill bits.
Preventing chips from entering the wall between the drill bit and the processed material is crucial for the quality of the hole. The shape and color of these chips can help the operator know whether the quality of the holes drilled by the drill bit is good or bad.
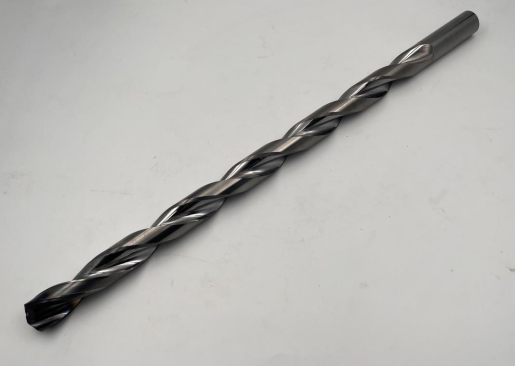
It is important for the chip removal groove of the drill bit to produce beautiful conical chips. Two to three curled or braided chips may wind up in the chip chute and rub and scratch both sides of the hole. This friction can cause surface roughness.
The back of the chip should be silver and shiny. Unlike the blue color you see during milling (because it means heat enters the chips, blue represents that your hole machining generates a large amount of heat on the cutting edge. This heat will cause the blade to wear faster.
Post time: Jul-07-2023